BAND
HEATER TERMINATIONS
Leads: |
 |
Fig.
1: Usual design for nozzle heating applications.
12" leads are standard. |
 |
Fig.
6: Flexible armor cable is the best solution
to lead abrasion problems. 12" armor with 14" overall length
leads are standard. Specify alternate position. |
 |
Fig.
3: Single conductor metal braid over lead
wire. Offers most practical solution to abrasion problem. 12"
braid with 14" overall length leads are standard. |
 |
Fig.
7: Double conductor metal braid exiting
from edge 180° from gap. |
 |
Fig.
4: Standard lead wires exiting 180° from
gap. |
 |
Fig.
16: Double conductor metal braid over lead
wires at same position as Fig. 5. 12" braid with 14" overall
length leads are standard. Specify alternate position. |
 |
Fig.
5: Leads exit at right angle to sheath
5/8" from gap. 12" lead wire in 3" long sleeving is
standard. Specify alternate position. |
|
|


MOUNTING CONFIGURATIONS

TERMINAL PROTECTION
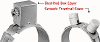 |
Terminal
Box Cover: 2" H x1-1/2" W x 2"
L. Also available in a 2-1/4" H x 2-1/16" W x 4-1/2"
L terminal box for larger clearance to terminals.
Ceramic Terminal Cover:
7/8" high x 3/4" O.D. for 10-24
thread. (PC4379-2; PC4380-1) |

PLUGS
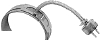 |
Fig.
7P: Plug can be attached to any lead configuration. |

EUROPEAN STYLE HIGH TEMPERATURE PLUG
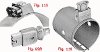 |
Fig.
110: Dimensions-3-1/2" H x 1-5/16"
L x 2-15/16" W
Fig. 115:
Dimensions-1-3/8" H x 3-7/16" L x 1-7/8" W
Fig. GQ8:
Receptacle (PC4396-3) |

Additional Variations
· Three terminal or lead, dual voltage, three phase or
ground
· Appliance pin terminals
· Full length fiberglass sleeving
· Rectangular or segment band
heatersprovide drawing
· Outside diameter design for
internally heating cylinder
· Stainless steel or Monel sheath
for use in corrosive atmosphere
· Metric Sizes
|

SPECIFICATION DATA
Watt Density
Termination
Figure |
Mounting
Figure |
Cold
Area |
Fig.
1 & 3 |
Fig.
9,10 or 20
Fig. 18,19 or 21 |
1" |
Fig.
1 & 3 |
Fig.
8 or 11 |
1"
if I.D. 4"
& width 3"
all other cases-3/4" |
Fig.
5,6 & 16 |
all |
1-3/8" |
Fig.
4 & 7 |
all |
1-3/4" |
T1 |
Fig.
9 & 10 |
1-1/2" |
T1 |
Fig.
8 |
1" |
T2 |
Fig.
9 & 10 |
1-1/8" |
T2 |
Fig.
8 |
1-3/8" |
T3 |
Fig.
8,9 & 10 |
1" |
I.D.
|
Standard Gap
|
>3/4"
- 5" |
1/4" |
>
5" - 10" |
1/2" |
>
10" - 16" |
3/4" |
>
16" |
1" |
|
Physical Limitations of Mica
Band Heaters
Full Band: 21-1/2" Maximum Diameter
Half Band: 43-1/2" Maximum Diameter
Termination |
Min.
Dia. |
Min
Width |
Figure |
Style |
Full
Band |
Half
Band |
1 |
Leads |
3/4" |
1-3/4" |
3/4" |
T1 |
Screw
Terminals |
1-1/2" |
2" |
1" |
T2 |
1-1/2" |
3" |
2-1/2" |
T3 |
1-1/2" |
3" |
1" |
3 |
Braided
Leads |
3/4" |
1-3/4" |
3/4" |
5 |
Leads |
1-1/2" |
3" |
1" |
6 |
Armor
Leads |
1-1/2" |
3" |
1" |
7P |
Armor
w/Plug |
1-1/2" |
3" |
1" |
8 |
Mounted
Flange |
3/4" |
1-3/4" |
3/4" |
11 |
Wedge
Mount |
1" |
-- |
3/4"
(6" max.) |
12 |
Hinged
Half Band |
-- |
1-3/4" |
1-1/2" |
16 |
Braided
Leads |
1-1/2" |
3" |
1" |
17 |
T1
& T3 |
1-1/2" |
-- |
1" |
T2 |
1-1/2" |
-- |
2-1/2" |
Leads |
1-1/2" |
-- |
3/4" |
110 |
EuroPlug |
3-1/2" |
-- |
1-1/8" |
115 |
EuroPlug |
4" |
-- |
2" |
Typical
Thickness is 5/32"
It is not recommended to use Mica Band
Heaters more than 3" wide. 1 - 3" wide heaters have
shown to be more efficient and economical. |
Recommended Maximum Watt Density
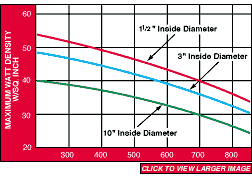
Steel
Block Temp in ºF
With SCR or SSR control output, watt density
can be increased up to 30%. |
Ordering Information:
· Catalog number if available
· Inside
Diameter and Width
· Wattage
and Voltage (resistance tolerance +
· 10%,
-5%). Cold resistance 6% lower than
· hot
resistance.
· If
Half Band, Wattage and Voltage each half
· Type
of termination, location and length of
· leads,
if applicable.
· Type
of mounting
· Submit
sketch or drawing if necessary
|
Maintenance and Trouble Shooting
1. Check Fit: The heater I.D. must be the same as the O.D. of the
cylinder.
2. Secure Firmly: To compensate for normal expansion, retighten periodically.
Cycling and normal metal expansion may cause the heaters to loosen.
3. Eliminate Contamination: Oil, plastic, dirt, etc., will carbonize
and shorten heater life.
4. Maintain Proper Voltage: The heater should be rated for the highest
voltage anticipated. Operation of a 220 Volt heater on 240 Volt
will raise the wattage by approximately 18%, increasing watt density
and reducing heater life.
5. Provide Proper Maintenance:
1. Tighten screw terminals firmly, but avoid excessive
pressure.
2. Protect leads from abuse and abrasion,
3. Maintain temperature controls and accessories in
good working condition to avoid over-temperature operating conditions.
6. Do not open one piece band heaters or internal damage may result.
If a Full Band Heater cannot be installed over the end of the cylinder,
then use a Split Case or Half Band Heater for best results.
7. Trouble Shooting: Check wiring for poor connections or open control
if heater fails to heat when initially energized. Sustained high
operating temperature may reduce heater life. If terminals oxidize,
tighten connections and check for proper wire size. |
|
Back
|
Home
|
Important Notice:
By purchasing products from this Site, you acknowledge and agree
that you have read and accept the Terms and Conditions of this online
store. For more information email us at: info@iprocessmart.com
|
|
|